solidworks flow simulation boundary conditions
I am new to flow simulation and am trying to simulate the flow of air through a constricted area with a couple small outlets. If the user neglects to assign a boundary condition at an opening then the.
Solidworks Flow Simulation Error Face Boundary
If you have another opening that takes 60 of the volume flow rate then why not define a pressure boundary condition there and a volume flow rate condition to the 40 opeing.
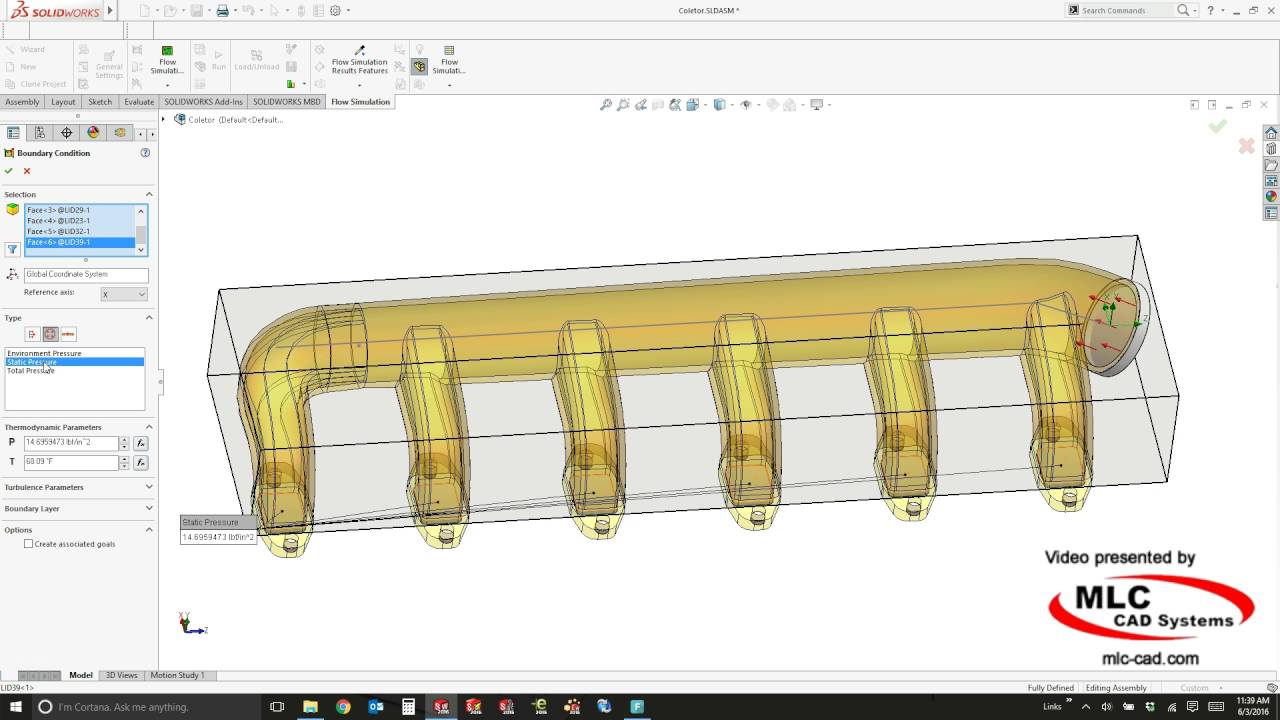
. SolidWorks Tips and Tricks. Set additional parameters that control how the analysis resolves the solidfluid interface curved surfaces narrow channels small solid features etc. This question has a validated answer.
With the full SOLIDWORKS Flow Simulation product you have the following advanced functionality. Usually when you receive the SOLIDWORKS Flow Simulation Error. If possible kindly help to explain using simple case studies.
Sets the face used for the inlet boundary. In Step 3 Specifying type of. By Suman Sudhakaran on January 7 2019.
I know air inlet air supply pressure is there a way to measure the conditions pressure and mass flow rates at the outlet. The last boundary condition that I want to add is a temperature to the entire body of the cube 125 C. You can apply these settings globally or for assemblies to a.
Learn methods and guidelines for using stereolithography SLA 3D printed molds in the injection molding process to lower costs and lead time. At the boundaries of an internal flow analysis in Flow Simulation one must specify the pressure from the outside fluid as either Static or Total depending on how the pressure was measured. In the Mass Flow Rate box set a value.
Applying Boundary Conditions in a Flow Study in SolidWorks. When I try define boundary conditions inlet volume flowenvironmental pressure on those particular ports I get the unresolved boundary condition warning when I run the simulation. I am performing flow analysis on a low speed low pressure high flow turbine pump and feel i have the entire concept of simulation wrong.
- Inlet pressure to 7 bar and outlet pressure to 1 bar. SOLIDWORKS Flow Simulation enables you and your team to simulate fluid flow heat transfer and fluid forces that are critical to the success of your product. Low-Volume Rapid Injection Molding With 3D Printed Molds.
- Inlet pressure to 7 bar and outlet flow to 0035 m3s. Setting up Flow Simulation boundaries and goals. It uses the SOLIDWORKS modeling engine to define the physical geometry and then the Flow Simulation environment defines boundary conditions and examines simulation results.
It runs into free air but i think it will be wrong to presume that the pressure at the exit lid will be 1 bar. With the CAD modeling complete I then turned to SOLIDWORKS Flow Simulation to study the aerodynamics. Face is not laying on the boundary between the solid and fluid region.
I do not have this type of trouble when the boundary conditions are set on the other inlets and I use one of the inlets as the outletand the simulation works fine. Insert Properties previously Insert Boundary Air Vents. In Step 2 Selecting results to transfer see image below browse to your original Flow Simulation project.
Although the majority of the boundary conditions are geometry-based the following boundary conditions remain mesh-based. Sets the temperature of the incoming fluid. Ill cover the boundary conditions shortly but at this point I could use a hand calculation to solve for the linear thermal expansion of the cube Figure 4.
The new home for the SOLIDWORKS Forum. Mach number Static pressure Total pressure. When I try to set boundary.
Hi every one I am havinng a small query regarding SolidWorks Flow Simulation Boundary condition. Although these two computational domain boundary conditions are set up by editing the default computational. I have tried to set.
In Step 1 Selecting Boundaries see below image select each Computational Domain boundary that you re-positioned earlier and Add this to the list of boundaries to transfer. In this article we set up and solved a flow problem from a solid model. Arrows from the face indicate the flow direction.
In Part 1 of this SOLIDWORKS Simulation blog I demonstrated how improper boundary conditions led to incorrect analysis results with Linear Thermal Expansion garbage in garbage out. SR By Sanjay Ramlall 052119. Faster Results with Boundary Conditions.
Hello I am seeking some general guidance on flow simulation in solidworks. SOLIDWORKS FloXpress remembers the initial selection in later calculations. For inlet and outlet.
The length along any edge is 100 mm and the change in temperature is 100 C. - Inlet flow to 0035 m3s and outlet pressure to 1 bar. You can set these boundary conditions.
Buy now Free trial Call. This question has a validated answer. Now lets look at what was happening under the hood with my analysis when applying temperature boundary conditions to a linear static study.
It is related to the geometry of the model assuming the boundary conditions are done correctly. Look for edge-edge or point-face contacts as they are considered invalid contacts under SOLIDWORKS. Symmetry and periodic boundary conditions in SOLIDWORKS Flow Simulation are used to reduce the size of the flow problem thereby reducing analysis run time.
In an atmosphere fluids in an open system will always encounter another fluid. Exclude from Warp previously Runner Element Filled Hot Runner. Then you have at least one pressure opeing and since the mass balance has the be fulfilled it will be by pushing in a certain mass through the pipes and sucking out a.
I have tried to run different simulation. Can anyone explain when to use Static pressure condition and when to use Environmental Pressure Boundary condition. Mass volume Volume flow Velocity.
Flow Simulation Boundary Conditions. Taking advantage of geometric symmetry by making use of symmetry boundary conditions in SOLIDWORKS Flow Simulation is a highly recommended best-practice technique for speeding up your flow analysis runs. Thanks for the help.
Uses flow rate mass as the flow metric. Set the initial temperature of a solid. Face to Apply Inlet Boundary Condition.
Discover how this hybrid manufacturing process enables on-demand mold fabrication to quickly produce small batches of thermoplastic parts. SOLIDWORKS Flow Simulation 2016 has capabilities for solving various flow and thermal problems.
Solidworks Flow Simulation Graphing Flow Variables Youtube
I Am A Beginner In Solidworks And My Project Was A Flow Simulation In A Papr Mask With Added Hepa Filter So That I Can Measure The Air Flow Rate To Compare
Solidworks Flow Simulation Real Wall And Ideal Wall Boundary Conditions Youtube
Faster Results With Boundary Conditions Trimech
Solidworks Simulation Using Symmetry
Flow Simulation Basic Concepts Engineers Rule
Solidworks Simulation Boundary Conditions And Linear Thermal Expansion Part 1 Solidworks Simulation Boundary Conditions And Linear Thermal Expansion Part 1
Common Mistake Done By Beginners In Flow Simulation In Solidworks Youtube
Faster Results With Boundary Conditions Trimech
Flow Simulation Basic Concepts Engineers Rule
Solidworks Simulation Boundary Conditions And Linear Thermal Expansion Part 1 Solidworks Simulation Boundary Conditions And Linear Thermal Expansion Part 1
Faster Results With Boundary Conditions Trimech
Flow Simulation Basic Concepts Engineers Rule
Go From Datasheets To Results With Solidworks Flow Simulation
Symmetry Boundary Conditions In Solidworks Flow Sim
Common Mistake Done By Beginners In Flow Simulation In Solidworks Youtube
Solidworks Flow Simulation Boundaries And Goals Youtube
Solidworks Tech Tip Simulation Productivity Tools Degree Of Freedom Dof Analysis Contact Visualization Plots The Solidapps Blog